A Century of Innovation in Thermal Spray Coatings
Thermal spray coatings have been around for over a century. The earliest thermal spray system is credited to a Swiss inventor, Max Ulrich Shoop, dating back to the late 1800s. These early systems were little more than oxyacetylene torches used to melt wire and spray coatings onto surfaces.
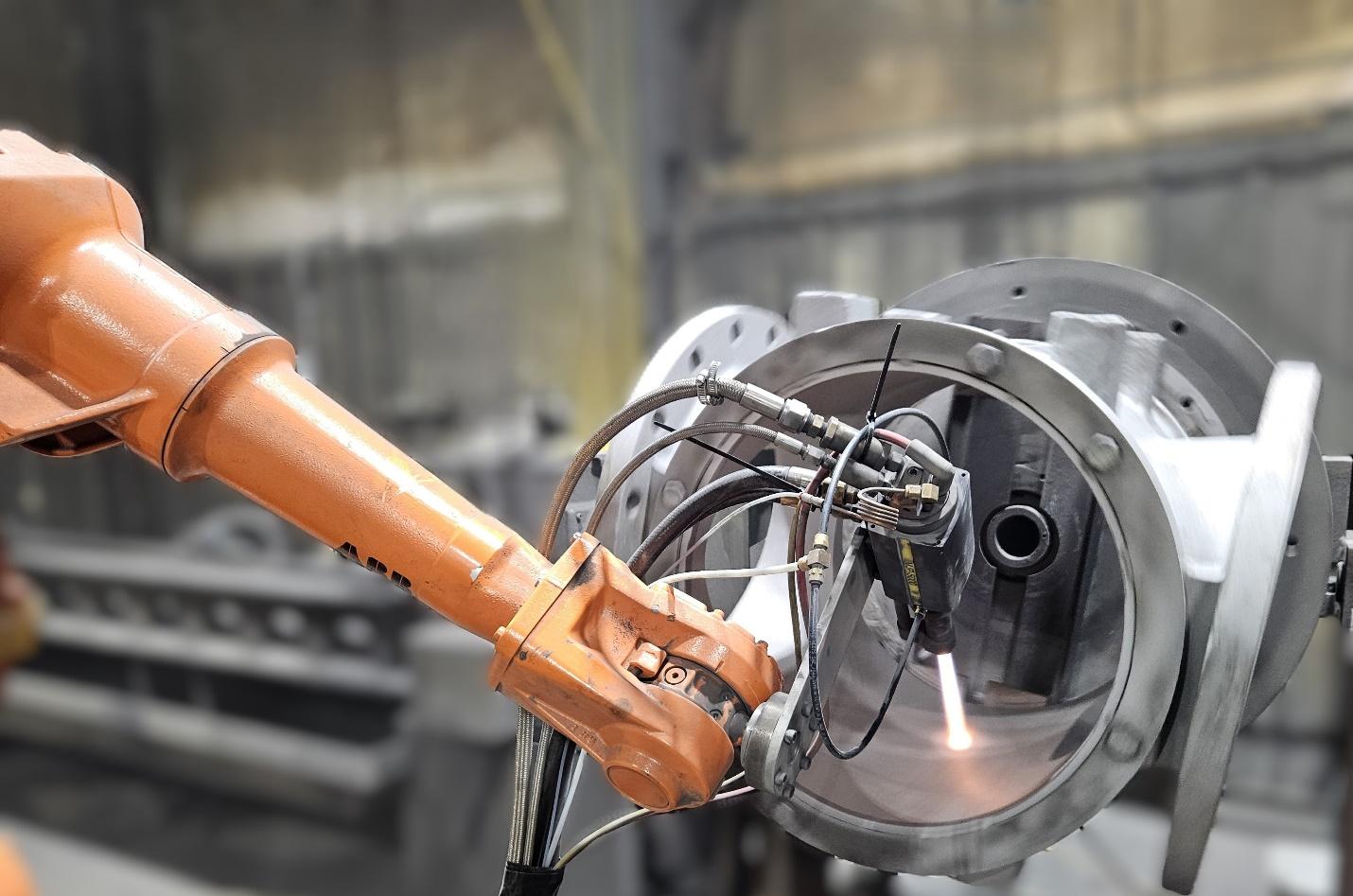
Fast forward 100 years, and James Browning pioneered the high-velocity thermal spray process in the early 1980s. Today, modern thermal spray coatings can be applied using a variety of advanced methods, including:
- High Velocity Oxygen Fuel / High Velocity Air Fuel (HVOF / HVAF)
- High Temperature Plasma
- Wire Arc
- Combustion with Molten Wire or Powder
- High Velocity Cold Spray
Precision is Everything: Controlling the Coating Process
A quality thermal spray coating depends on precisely controlled variables such as fuel mix, gas flows, and feedstock delivery. Beyond that, the physical geometry of the part, standoff distance, spray angle, and traverse speed all affect coating quality. Even small adjustments can significantly alter the final coating properties. Once you dial in the perfect “recipe,” consistency becomes the priority.
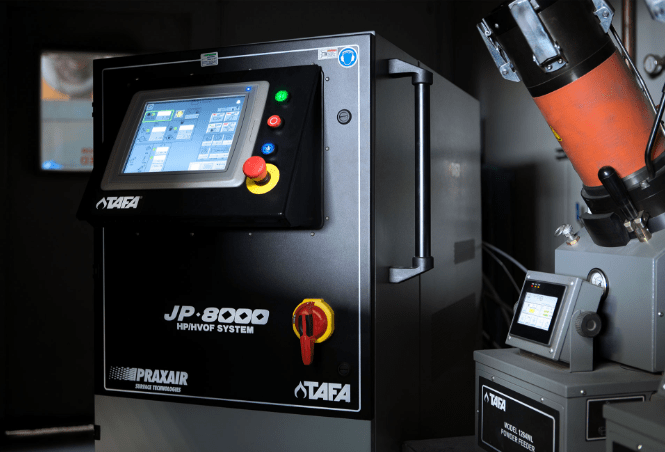
Common Types of Thermal Spray Coating Application
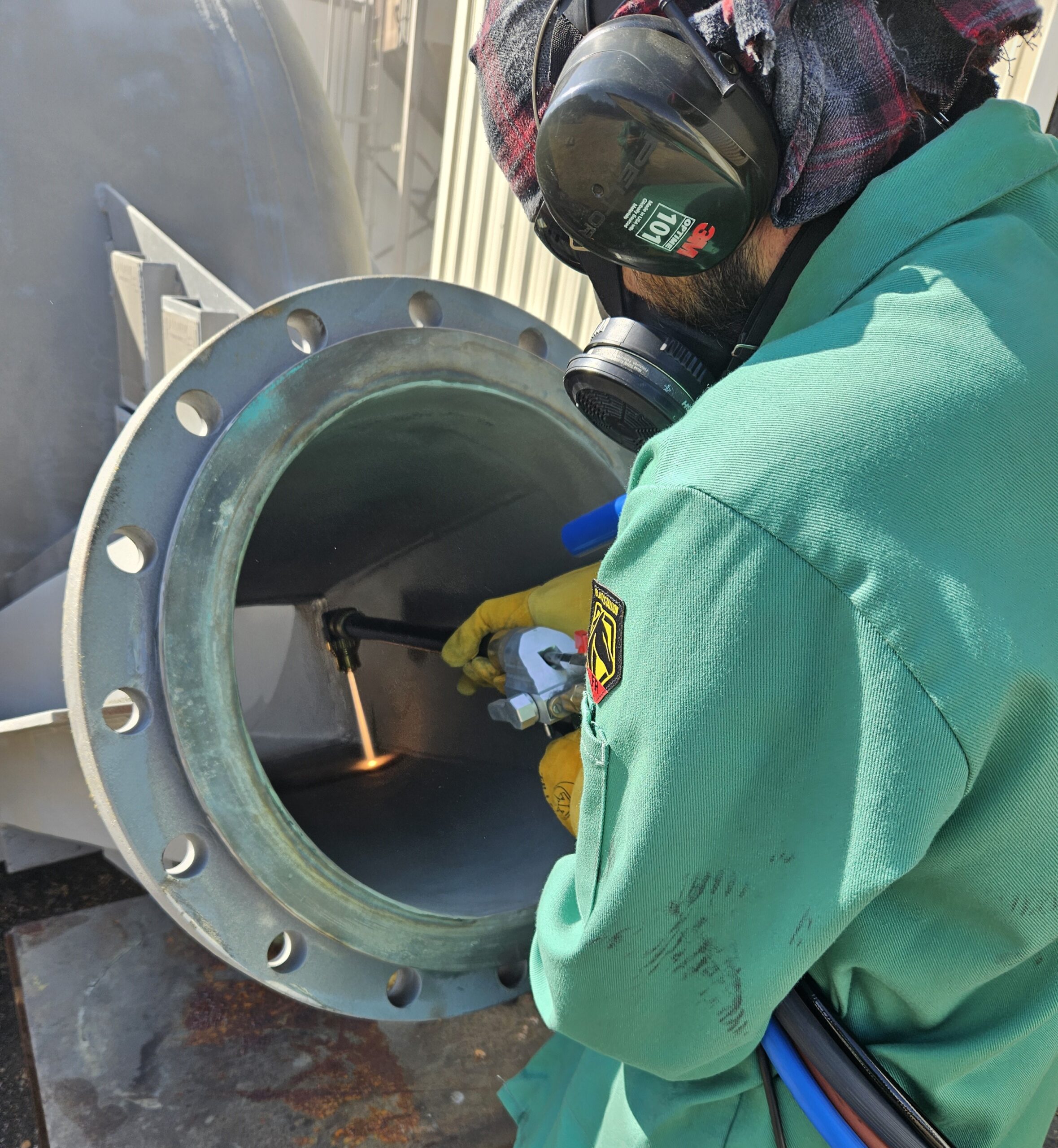
Hand Spraying
Originally, coatings were applied manually by hand spraying—an incredibly versatile method suitable for flat surfaces and rotating round parts. When done by experienced operators, this can result in good coatings. However, it remains dependent on human performance and endurance, which can fluctuate.
Linear Actuation
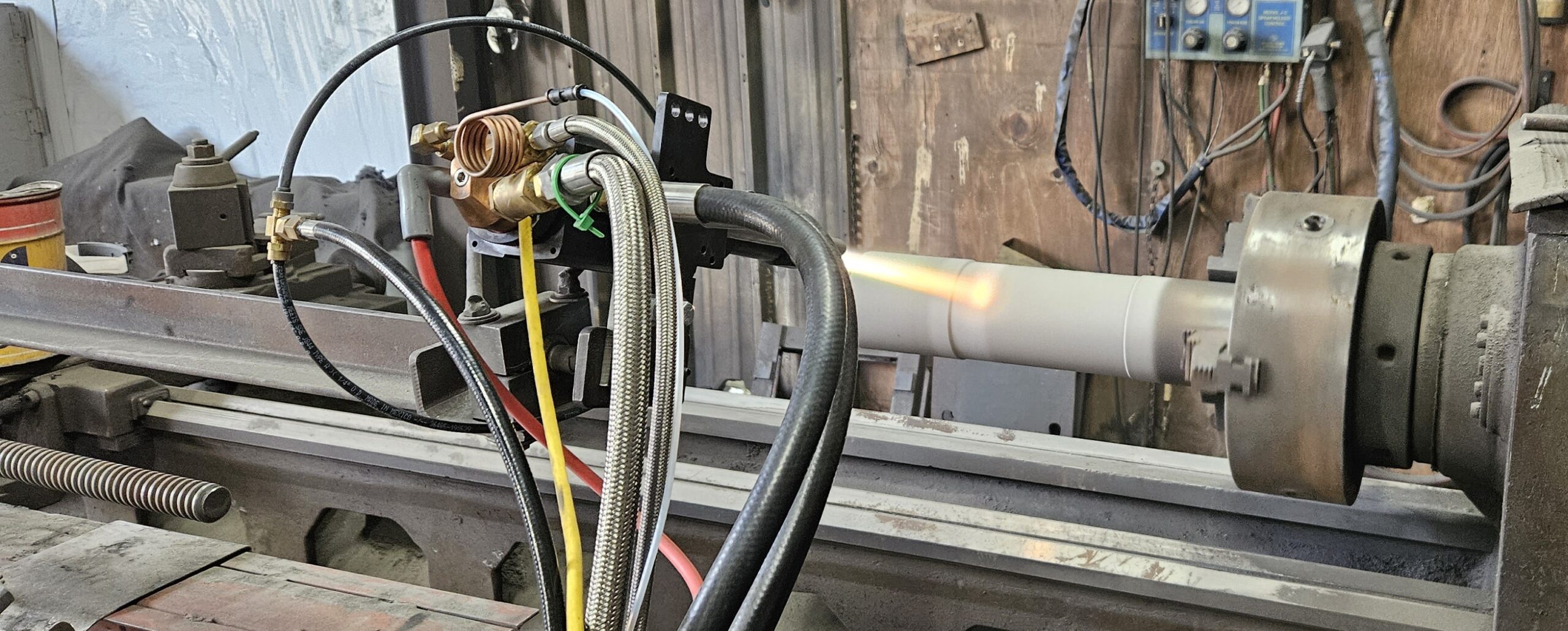
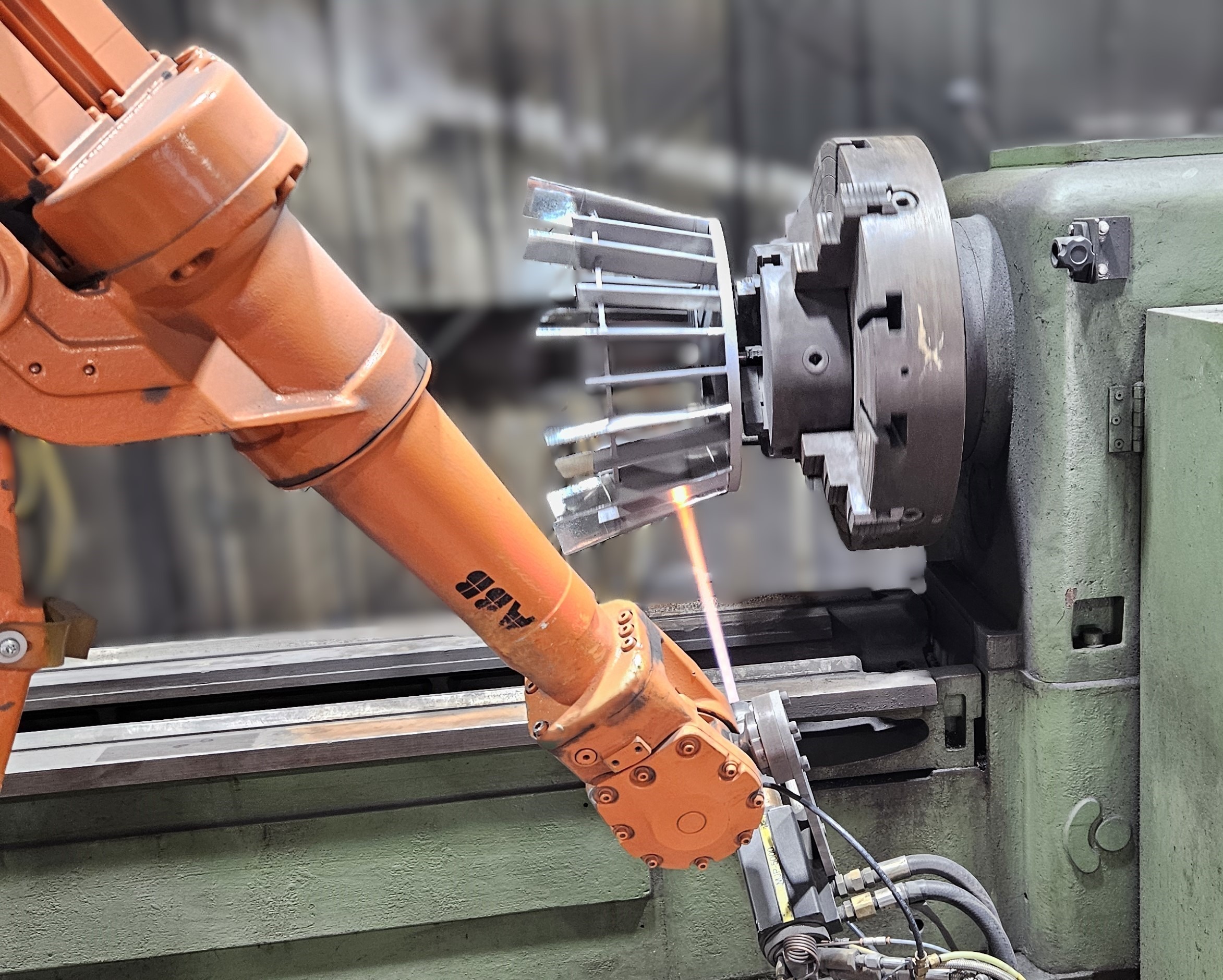
Robotic Precision
Engineering Coatings at the Microscopic Level
Robotic control allows engineers to fine-tune coatings for specific performance needs. Adjusting surface speed, overlap, and temperature settings can influence microstructure—enhancing characteristics like bond strength, porosity, and hardness. These microscopic details are essential in meeting the demands of critical applications.
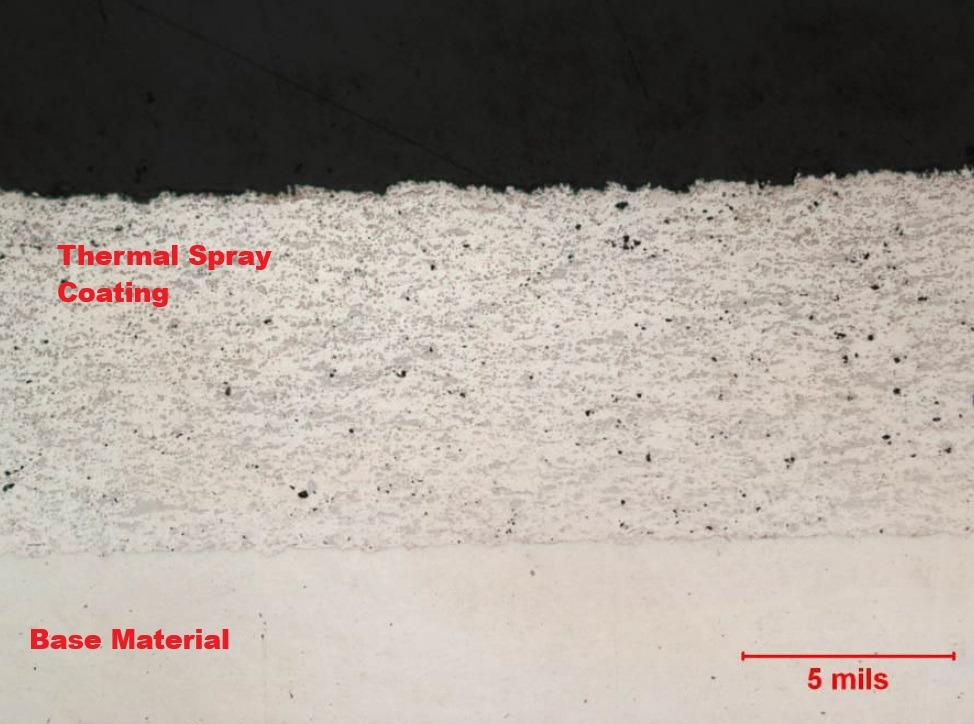
My Journey with Robotic Coating Technology
As a Thermal Spray Engineer, I’ve dedicated my career to mastering robotic thermal spray processes across industries like aerospace, oil and gas, automotive, and power generation. In late 2023, I joined Palmer Tool to transform thermal spray from a side offering to a core service.
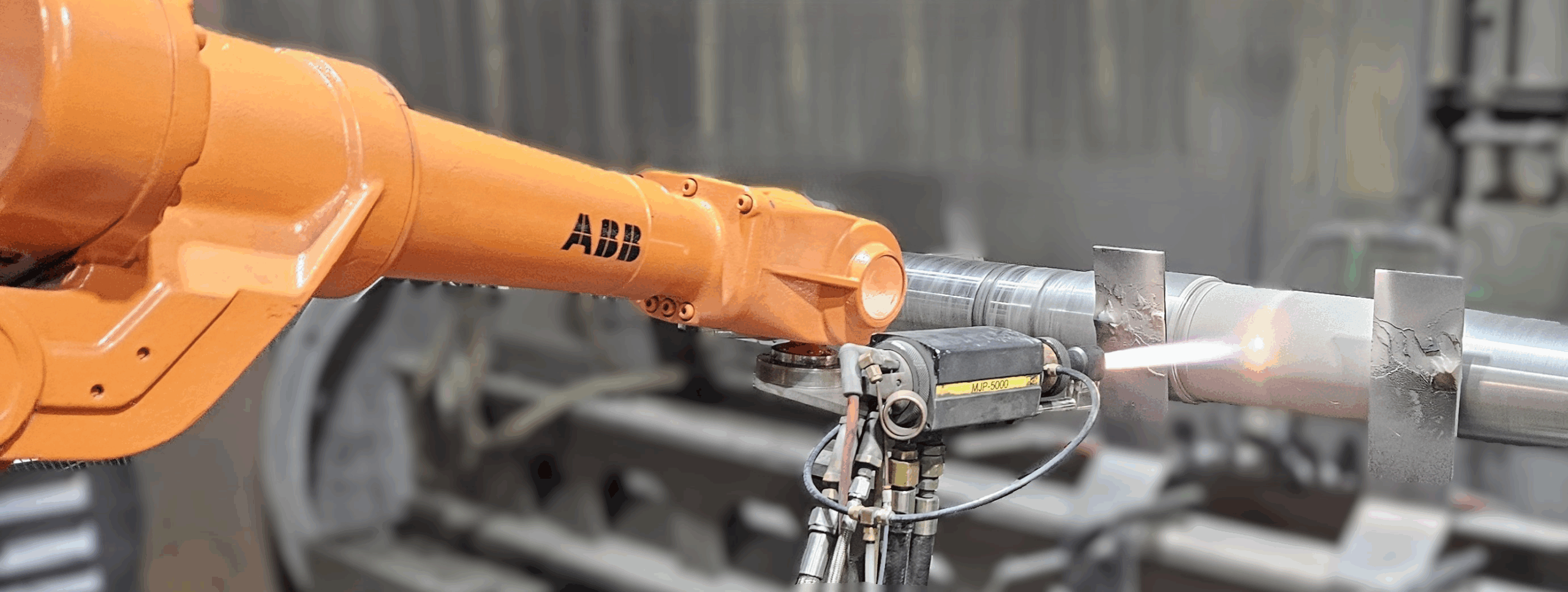
A New Era at Palmer Tool
I’m proud to share that we’ve recently deployed an ABB IRB 2600 6-axis Industrial Robot, fully integrated with our Praxair JP8000 HVOF coating system. We’re scaling our capabilities rapidly and taking on new challenges with confidence and precision.
Let’s Build Something That Lasts
With my expertise and Palmer Tool’s dedicated team, we’re ready to develop custom coating solutions that improve part performance and longevity—no matter how demanding the application.
Contact us today to see what Palmer Tool can do for you
Director of Thermal Spray