HVOF THERMAL SPRAY & HARD FACING
The Premier HVOF High Performance Coating Service In The Southeast.
High Performance Coatings
Are you tired of continuously replacing your process components time and time again?
Do you find yourself “caught between a rock and a hard place” of juggling your short-term budget limitations vs. maintaining your equipment with a long-term “cost of ownership” approach?
Do yourself a favor – don’t replace your high-wear components before FIRST speaking with Palmer Tool about the potential benefits of HVOF or PTA to EXTEND the service life of your equipment.
HVOF &
THERMAL SPRAY
Customers in Tennesse, and all of the Southeast depend on Palmer Tool for their High-Velocity Oxygen Fuel (HVOF) coatings.
HVOF is a thermal spray coating process that improves a component’s surface properties and extends equipment life by protecting against wear and corrosion.
Custom applications that frequently benefit from HVOF coatings include chemical processing, mining, power generation, oil and gas, cement/asphalt, steel mills, pulp and paper mills, hydraulic and pneudraulics components, particle reduction or recycling, rotary airlocks, and many more.
The HVOF process involves feeding a mixture of fuel and oxygen into a combustion chamber, where they are ignited and continuously combusted. The resultant hot gases flows through a converging–diverging nozzle and enters a straight-walled barrel section. A powder feed stock is then injected into the gas stream where it is accelerated through a barrel. The stream of hot gas and powder exits the barrel with a jet velocity exceeding Mach 3.
The resulting jet stream is sprayed directly onto the surface of the component, where it begins to deposit as the powder embeds into the substrate. The tremendous kinetic energy of the powder impacting the surface results in low porosity, high bond strength, compressive residual stress, and relatively low processing temperatures. This allows for temperature sensitive materials such as high strength steels, titanium alloys, and high strength aluminum alloys to be coated without losing their material properties.
HVOF coatings range in thickness from 0.1mm – 0.8 mm (0.030″) or more and offer the benefits of extreme wear and corrosion resistance. Common coating powders include Stellite, Colmonoy, Tungsten-Carbide, Chrome Carbide, Stainless Steels, Inconel, Triaballoy and many other alloys with hardness values ranging from 35 HRC (350HV Vickers) to 71.5 HRC (1200 HV Vickers).
HVOF applied Tungsten Carbide is the chosen coating process to replace Electrolytic Hard Chrome Plating for civilian and military aerospace applications. HVOF coatings may also be ground and superfinished to meet all bearing and seal surface finish requirements.
Customer applications which frequently benefit from PTA welding include chemical processing, dry powders, mining, power generation, oil and gas, cement/asphalt, steel mills, pulp and paper mills, particle reduction or recycling, rotary airlocks or other rotating components, and many more. The Plasma Transferred Arc process (also known as PTA) is a welding process that applies wear and corrosion resistant layers (hard-facing) onto metal surfaces.
The hard-facing can be done with superalloy materials (in wire or powder form), such as Stellite 6 or Colmonoy 88. In addition to hard-facing, softer alloys and carbide composites can be used to achieve diverse properties such as improved mechanical strength, wear resistance, galling resistance, and corrosion resistance.
The PTA process is characterized by a high density Plasma Arc, obtained by ionization of Argon gas passing through an electric arc to serve as a shield. A second electric arc (Transferred Arc) is produced simultaneously to provide the energy needed to melt both the base metal and the filler metal/powder.
The transferred arc is “throttled” to further increase the temperature, obtaining a plasma column temperature between 14,000°F (8,000°C) and 32,000°F (18,000°C). After the plasma column passes and the base and filler metals re-solidify, a substance-to-substance bond between the filler material and the base material is created. Because PTA utilizes a constricted, columnar welding arc, the heat input is highly localized. This allows full fusion of the overlay material, while introducing minimum heat into the part.
PTA especially excels applying powder alloys that are too hard to draw into wire, such as various cobalt and metal matrix composites. PTA is normally more economical than laser (lower operating and equipment cost), GTAW or TIG. Its lower heat input allows the process to achieve the required overlay properties in a thinner layer, and alloys are often less expensive in powder form vs wire.
The capability of producing a low dilution, low porosity, thin overlay allows the PTA process to achieve a higher quality product using much less material and with drastically less heat input into the base material.
Advantages of Plasma Transfer Arc Welding over other hard-facing processes include…
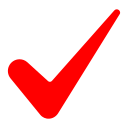
Limited heat addition to base metal (due to constricted and columnar welding arc combined with high working speed)
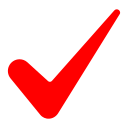
Maintain structural quality and metallurgic homogeneity of base metal
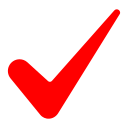
(controlled penetration, with precise positioning of weld deposits on a single pass)
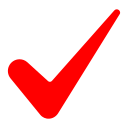
High working speed (often 2X – 3X faster than MIG or TIG) reduces heat addition to base metal and lowers operating cost
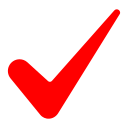
Better wear resistance due to harder, tougher coatings
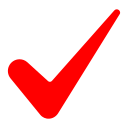
Improved corrosion protection due to less porosity
Advantages of HVOF spraying over other thermal spray processes include…
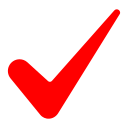
Higher density (lower porosity) due to greater particle impact velocities
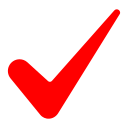
Higher strength bond (both to the underlying substrate and within the coating)
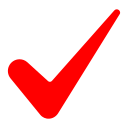
Lower oxide content due to less in-flight exposure time
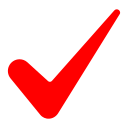
Retention of powder chemistry due to reduced time at temperature
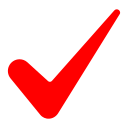
powder sizes
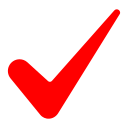
Compressive residual stress ensuring coating integrity in high stress applications
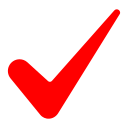
Better wear resistance due to harder, tougher coatings
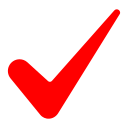
Higher hardness due to less degradation of carbide phases
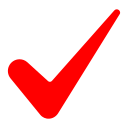
Improved corrosion protection due to less porosity
PLANT SHUTDOWNS &
AFTER-HOURS EMERGENCY SUPPORT
Discover How Robotics Works
in Thermal Spray Coatings
Certified Professsionals
Certified Professsionals

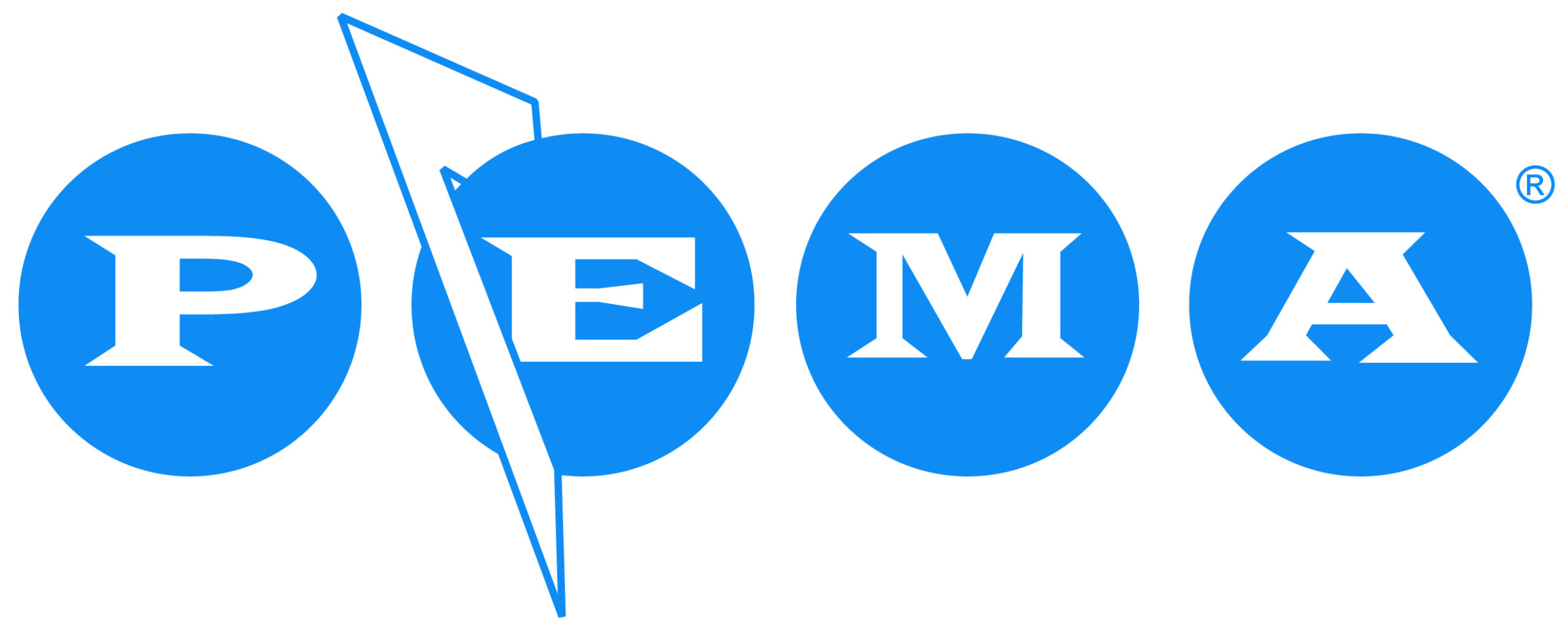
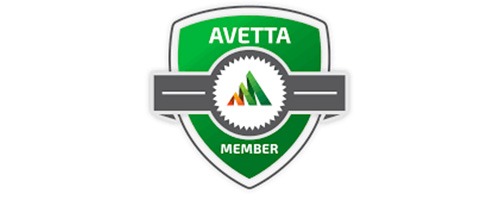
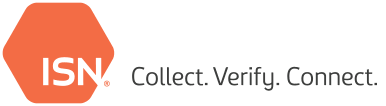
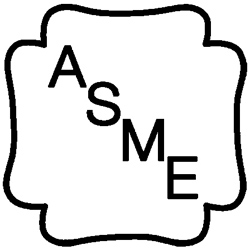
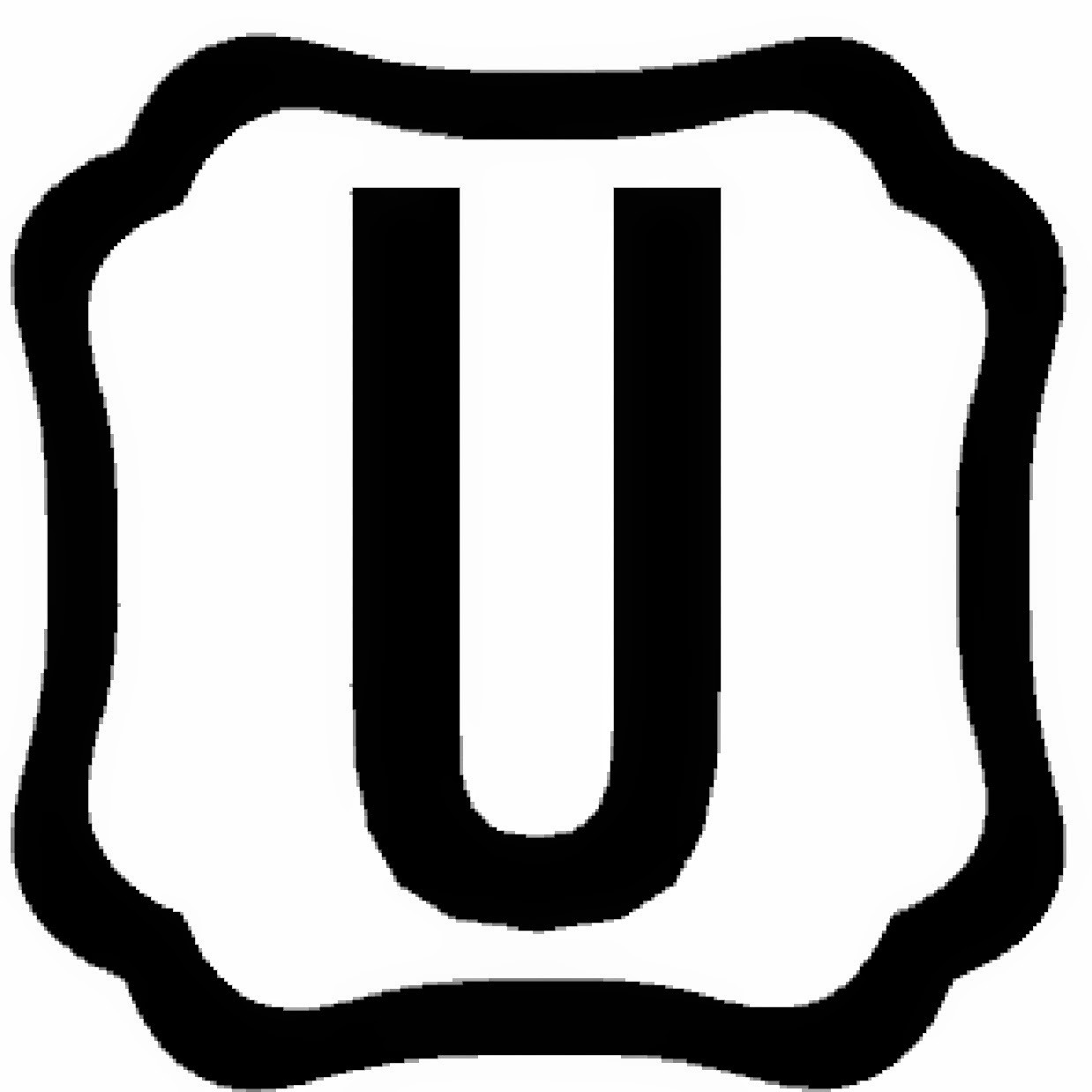
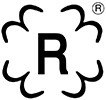
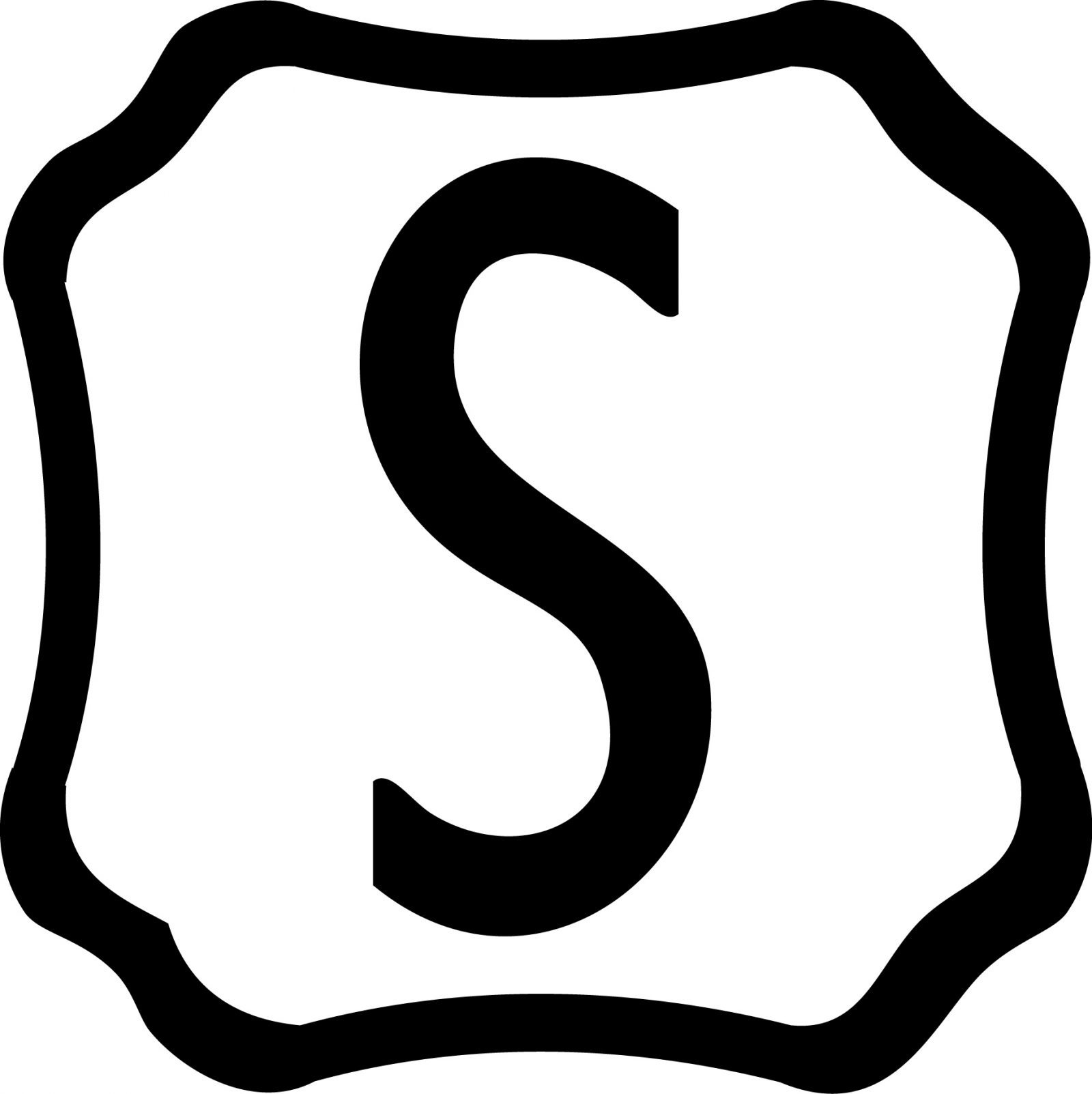
Trusted by Industrial Partners ...
They are great people to deal with high quality workmanship
- Mike Corbitt
Get A Quote