In the oil and gas industry, the use of hardfacing techniques has become increasingly important for enhancing the performance and durability of drilling components and other critical equipment.
Hardfacing involves applying a layer of high-hardness material over a substrate to provide superior wear resistance and protection against corrosion.
This article explores the various benefits of hardfacing in the oil and gas industry and highlights the key techniques and materials used in this process.
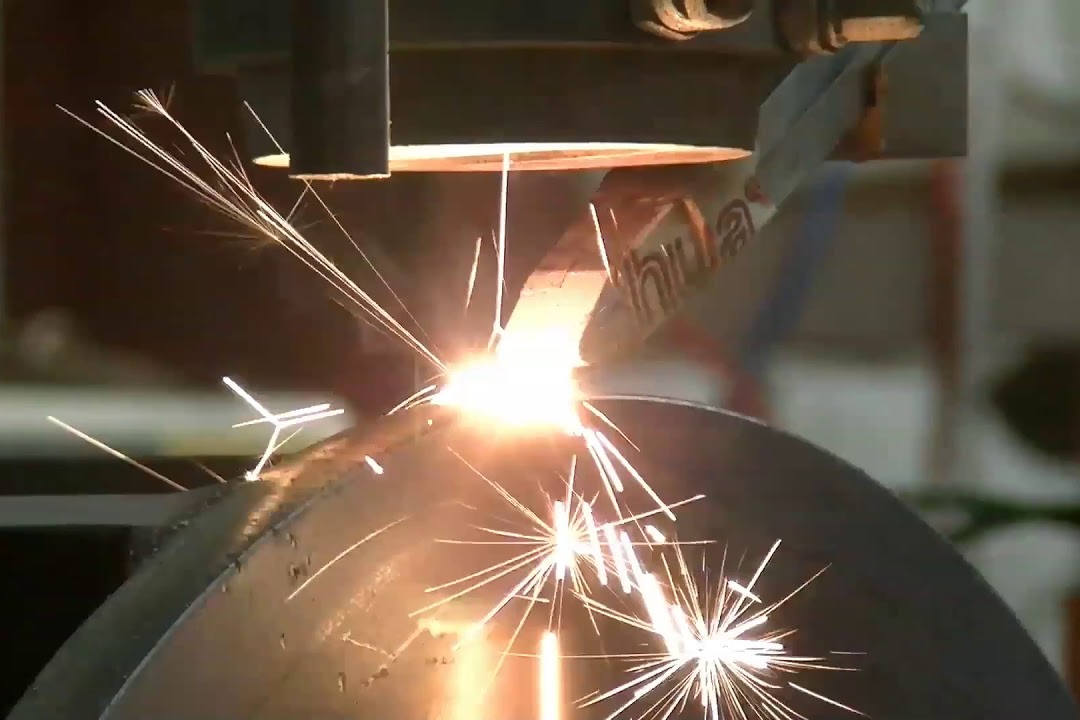
The Importance of Hard-facing in the Oil and Gas Industry
Enhancing Wear Performance
One of the primary benefits of hardfacing in the oil and gas industry is the significant improvement in wear performance. The high-hardness materials used in hardfacing, such as Tungsten Carbide, provide superior resistance to abrasion, erosion, and impact. This is particularly crucial for drilling components that are exposed to intense wear and tear during drilling operations. By hardfacing these components, their lifespan can be extended, reducing maintenance costs and downtime.
Minimizing Heat-Induced Distortion
Another advantage of using hardfacing techniques, specifically laser hardfacing, is the ability to minimize heat-induced distortion. Unlike conventional techniques like GMAW, TIG, or PTA, laser hardfacing delivers a concentrated and controlled heat source, resulting in minimal distortion of the substrate material. This is particularly important for components with complex geometries or critical dimensional tolerances, ensuring that they retain their original shape and functionality.
Reducing Heat Affected Zone (HAZ)
Hardfacing in the oil and gas industry also offers the benefit of reducing the heat-affected zone (HAZ) during the deposition process. The HAZ refers to the area of the base material that experiences changes in microstructure and mechanical properties due to the heat input during welding or cladding. By utilizing hardfacing techniques, such as laser cladding, the localized heat input minimizes the HAZ, resulting in improved metallurgical properties and reduced risk of cracking or distortion.
Techniques for Oil and Gas Hardfacing
Laser Hardfacing
Laser hardfacing is a highly effective technique used in the oil and gas industry for its precision and control. This method involves using a high-power laser beam to melt the surface of the component and simultaneously feed a hardfacing powder material. The laser beam provides precise heat control, allowing for minimal dilution and quick solidification of the deposited material. Laser hardfacing offers several advantages over conventional techniques, including higher hardness of the coating material, minimal heat-induced distortion, and reduced HAZ.
GMAW, TIG, and PTA Techniques
In addition to laser hardfacing, other conventional techniques are also employed in the oil and gas industry for hardfacing applications. Gas Metal Arc Welding (GMAW), Tungsten Inert Gas (TIG) welding, and Plasma Transferred Arc (PTA) welding are commonly used methods. These techniques involve the deposition of hardfacing materials using a welding arc or plasma arc. While these methods may not offer the same precision and control as laser hardfacing, they are still effective in certain applications and can provide satisfactory wear resistance properties.
Materials Used in Oil and Gas Hardfacing
Tungsten Carbides
Tungsten Carbide is a popular choice for hardfacing in the oil and gas industry due to its exceptional hardness and wear resistance. It is available in various forms, including spherical and angular particles, and can be applied using different hardfacing techniques. Tungsten Carbide coatings are particularly effective in protecting drilling components, such as drill bits, stabilizers, and reamers, from abrasive wear caused by contact with rocks and drilling fluids.
Cobalt-based Alloys
Cobalt-based alloys, such as Stellite 6 and Stellite 21, are widely used in hardfacing applications for their excellent resistance to erosive and corrosive wear. These alloys exhibit high toughness and can withstand extreme operating conditions in the oil and gas industry. Cobalt-based alloys are often applied to components that are exposed to severe abrasion, erosion, and corrosion, such as valves, pumps, and impellers.
Nickel-based Alloys
Nickel-based alloys, such as Colmonoy 56 and Colmonoy 88, are commonly employed in hardfacing applications where resistance to high-temperature wear, corrosion, and oxidation is crucial. These alloys offer excellent mechanical properties, including high strength and toughness, making them suitable for components operating in aggressive and high-temperature environments, such as downhole tools, valves, and pumps.
Corrosion Resistant Coatings
In addition to wear resistance, hardfacing techniques also provide significant benefits in terms of corrosion resistance. Laser cladded corrosion resistant coatings, in particular, offer unique advantages compared to traditional coating techniques. The localized heat input during laser cladding results in minimal dilution of the base materials, which is especially important for iron substrates. Lower dilution reduces the coating thickness requirements, resulting in cost savings while still providing effective corrosion protection.
Internal Diameter (ID) Cladding
Apart from protecting external surfaces, hardfacing techniques can also be applied to the internal diameters of components through a process known as ID cladding. This technique involves depositing a wear-resistant coating onto the inner surface of pipes, tubes, or other cylindrical structures. ID cladding is essential for components that come into contact with corrosive fluids or abrasive particles, providing a protective barrier and extending the service life of the equipment.
ID Cladding Capabilities
The Palmer Tool Company, a leading provider of hardfacing solutions, offers extensive ID cladding capabilities. Their equipment allows for cladding internal diameters as small as 3.5 inches with lengths up to 40 inches, and even greater lengths can be accommodated upon request. This capability enables the hardfacing of critical components used in the oil and gas industry, such as downhole tools, pipes, and valves.
Expertise in Various Coating Materials
The Palmer Tool Company specializes in working with a wide range of coating materials for ID cladding applications. Their expertise extends to spherical and angular Tungsten Carbides, cobalt-based alloys, and nickel-based alloys. By understanding the unique requirements of each application, their team of experts can recommend and apply the most suitable coating material to achieve optimal wear and corrosion resistance.
Hardfacing techniques play a crucial role in enhancing the performance and durability of components in the oil and gas industry. By depositing wear-resistant coatings using methods like laser hardfacing, GMAW, TIG, or PTA, the wear performance of drilling components can be significantly improved. Various materials, including Tungsten Carbides, cobalt-based alloys, and nickel-based alloys, are used to provide superior wear and corrosion resistance. Additionally, laser cladded corrosion resistant coatings offer unique advantages by minimizing dilution and reducing coating thickness requirements. With companies like Palmer Tool Company specializing in high power laser-based solutions, the oil and gas industry can benefit from extended equipment lifespan, reduced maintenance costs, and improved operational efficiency.